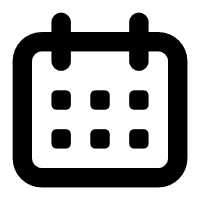
电子设备日益向小型化、高性能化发展的今天,电路板作为电子系统的核心载体,其性能的优劣直接影响着整个设备的运行质量。电路板镀膜技术,作为提升电路板性能的重要手段,正受到越来越多的关注。它通过在电路板表面覆盖一层或多层特定材料的薄膜,赋予电路板新的功能特性,如增强导电性、提高抗氧化能力、改善可焊性等,在保障电子设备稳定运行、延长使用寿命等方面发挥着关键作用。
电路板在使用过程中,会面临各种复杂的环境因素,如潮湿的空气、腐蚀性气体、灰尘等。这些因素会逐渐侵蚀电路板表面的金属线路,导致铜箔氧化、线路腐蚀,进而引发电路故障。镀膜能够在电路板表面形成一层致密的保护膜,有效隔绝外界环境与电路板的直接接触,减缓金属的氧化和腐蚀速度。例如,在沿海地区或化工企业周边等环境恶劣的场所,经过镀膜处理的电路板,其使用寿命可比未镀膜的电路板延长数倍。
部分镀膜材料具有良好的导电性,通过在电路板表面镀上这些材料,可以降低线路电阻,提高信号传输的效率和稳定性。在高频电路中,信号传输速度快、频率高,对线路的阻抗匹配要求极高。合适的镀膜能够优化线路的阻抗特性,减少信号反射和损耗,确保高频信号的高质量传输。此外,一些镀膜还具有绝缘性能,可以在电路板上形成绝缘层,隔离不同电位的线路,防止短路现象的发生,进一步提升电路板的电气可靠性。
在电路板组装过程中,良好的可焊性是确保电子元件与电路板可靠连接的关键。然而,电路板表面的氧化、污染等问题会降低其可焊性,导致焊接不良、虚焊等缺陷。镀膜可以去除电路板表面的氧化物,形成一层易于焊接的表面层,提高焊料与电路板之间的润湿性和结合力,使焊接过程更加顺利,提高组装效率和产品质量。
化学镀镍金是目前电路板行业应用较为广泛的镀膜工艺之一。该工艺首先通过化学镀的方法在电路板表面沉积一层镍层,镍层厚度一般在3-5μm。镍层具有良好的耐磨性和耐腐蚀性,能够为电路板提供初步的保护。同时,镍层的存在可以防止铜向金层扩散,避免金层变色和性能下降。在镍层之上,再通过置换反应沉积一层金层,金层厚度通常在0.05-0.1μm。金层具有优异的抗氧化性、导电性和可焊性,能够有效保护镍层,并且在电子元件焊接过程中,金层能够迅速溶解在焊料中,实现良好的焊接效果。化学镀镍金工艺适用于对表面平整度、可焊性和可靠性要求较高的电路板,如计算机主板、手机电路板等。
化学镀镍钯金工艺是在化学镀镍金工艺的基础上发展而来的。与ENIG工艺相比,它在镍层和金层之间增加了一层钯层,钯层厚度一般在0.05-0.1μm。钯层的加入可以有效抑制“黑盘”现象的发生。“黑盘”现象是指在ENIG工艺中,由于镍层表面的磷含量不均匀或在高温、高湿环境下,镍层与金层之间发生化学反应,导致镍层表面变黑,从而影响焊接性能和电路板的可靠性。ENEPIG工艺中的钯层能够阻止镍与金之间的不良反应,提高镀膜的稳定性和可靠性。该工艺适用于对可靠性要求极高的领域,如航空航天、医疗设备等。
有机可焊性保护膜是一种在电路板表面涂覆有机薄膜的镀膜工艺。OSP膜厚度极薄,通常在0.2-0.5μm。它通过化学方法在铜表面形成一层透明的有机膜,这层膜能够在一定时间内保护铜不被氧化,同时在焊接时能够迅速分解,不影响焊接效果。OSP工艺具有成本低、工艺简单、环保等优点,适用于对成本敏感且对可焊性有一定要求的电路板,如消费电子、普通家电等领域的电路板。但OSP膜的抗氧化能力相对较弱,储存时间有限,一般需要在涂覆后较短时间内完成焊接组装。
沉银工艺通过置换反应在电路板表面沉积一层薄银层。银层具有优异的导电性(仅次于金)和可焊性,能有效降低线路电阻,提升信号传输性能。但银层化学稳定性较差,易氧化或硫化,因此常需涂覆有机保护剂或进行浸金处理以延长寿命。该工艺适用于高频电路(如5G、卫星通信设备),但在高湿/高硫环境中需谨慎设计,避免银迁移或腐蚀。
前处理是电路板镀膜的基础步骤,其目的是去除电路板表面的油污、氧化物、灰尘等杂质,使电路板表面达到清洁、活化的状态,为后续的镀膜工艺提供良好的基础。前处理通常包括除油、微蚀、酸洗、水洗等工序。除油工序使用碱性或有机溶剂去除电路板表面的油污;微蚀工序通过化学腐蚀的方法去除电路板表面的氧化层和轻微的毛刺,增加表面粗糙度,提高镀膜与电路板之间的结合力;酸洗工序用于进一步去除金属表面的氧化物,并调整表面的酸碱度;水洗工序则用于清洗去除前几道工序中残留的化学试剂。
根据不同的镀膜类型,采用相应的镀膜工艺进行镀膜。以化学镀镍金为例,在完成前处理后,将电路板浸入含有镍盐、还原剂、络合剂等成分的化学镀镍溶液中,在合适的温度(一般为80-90℃)和pH值(通常为4.5-5.5)条件下,镍离子在电路板表面被还原剂还原,沉积形成镍层。镀镍完成后,将电路板转移到镀金溶液中,通过置换反应在镍层表面沉积金层。在镀膜过程中,需要严格控制溶液的成分、温度、pH值、时间等工艺参数,以确保镀膜的厚度、均匀性和质量符合要求。
后处理主要包括水洗、干燥、检测等工序。水洗用于去除电路板表面残留的镀膜溶液和化学试剂,防止其对电路板性能产生不良影响;干燥则是将电路板表面的水分去除,避免水分残留导致电路板生锈或其他质量问题;检测工序通过各种检测手段,如外观检查、膜厚测量、可焊性测试、导电性测试等,对镀膜的质量进行全面评估,确保镀膜后的电路板满足设计要求和使用标准。
采购咨询,获取商机