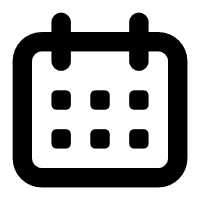
现代制造业,沉金工艺与镀金工艺作为常见的表面处理手段,广泛应用于提升产品的美观度、耐腐蚀性和导电性等性能。然而,这两种工艺在成本构成上存在显著差异,深入了解这些差异对于企业合理选择工艺、控制生产成本、提升市场竞争力具有重要意义。
沉金工艺,通常指化学沉金,是利用化学氧化还原反应,在基底材料,如PCB板的铜表面上沉积一层金。其原理是在含有金盐的溶液中,通过特定的还原剂使金离子还原并均匀地沉积在基底表面。这个过程不需要外加电流,相对较为温和,对设备的要求相对简单。不过,沉金工艺需要精确控制溶液的成分、温度、pH值等参数,以确保金层的质量和厚度均匀性。由于沉金过程相对较慢,需要较长的处理时间来达到理想的金层厚度,这在一定程度上增加了时间成本。
镀金工艺主要通过电解原理实现。在电解池中,将待处理的工件作为阴极,金作为阳极,置于含有金离子的电解液中。当电流通过时,金离子在阴极得到电子被还原成金原子并沉积在工件表面。这种工艺能够快速地在工件表面镀上较厚的金层,生产效率相对较高。但电解过程需要专门的电源设备,对设备的精度和稳定性要求较高,设备的购置和维护成本也相应增加。
从金材料的使用量来看,镀金工艺通常需要更多的金。由于镀金能够实现较厚的金层沉积,其厚度范围一般在0.1-2.5μm之间,相比之下,沉金工艺得到的金层较薄。例如,在PCB板的应用中,沉金工艺的金层厚度一般在0.05-0.15μm左右。随着金层厚度的增加,镀金工艺所需的金材料量呈线性增长。而且,在电解过程中,为了保证金离子的持续供应和电镀效果的稳定性,电解液中的金离子浓度需要维持在一定水平,这意味着在生产过程中会有更多的金材料被消耗。
此外,金材料的价格波动对两种工艺成本影响程度不同。沉金工艺由于金材料使用量相对较少,在面对金价波动时,成本变动相对较小。而镀金工艺,由于大量依赖金材料,金价的任何波动都会对其成本产生显著影响。例如,当国际金价大幅上涨时,镀金工艺的成本会迅速攀升,给企业带来较大的成本压力。
沉金工艺所需的设备相对简单,主要包括反应槽、溶液循环系统、温控装置等。这些设备的初始购置成本相对较低,并且在日常运行中,维护成本也不高。由于工艺过程相对稳定,对操作人员的技术要求主要集中在对溶液参数的监控和调整上,人员培训成本较低。
镀金工艺则需要专门的电镀电源、整流器、电镀槽以及复杂的过滤和循环系统等设备。这些设备不仅价格昂贵,而且在运行过程中需要消耗大量的电能,设备的折旧和能耗成本较高。同时,电解过程对工艺参数的控制要求极为严格,如电流密度、电压、电镀时间等,任何一个参数的偏差都可能导致金层质量问题。这就要求操作人员具备较高的专业技能和丰富的经验,人工培训成本和人力成本都较高。
在实际生产中,还有一些其他因素会影响两种工艺的成本。例如,沉金工艺在溶液配制和维护过程中,需要使用多种化学试剂,这些试剂的成本虽然相对金材料较低,但长期累积下来也是一笔不小的开支。而且,沉金过程中产生的废水含有重金属和化学物质,需要进行专门的处理以达到环保排放标准,废水处理成本也不容忽视。
镀金工艺在电镀过程中,可能会因为工艺控制不当出现金层质量问题,如金层附着力不足、厚度不均匀等。一旦出现这些问题,工件往往需要返工处理,这不仅增加了材料和时间成本,还可能导致生产效率下降。另外,镀金工艺对生产环境的要求较高,需要保持车间的清洁度和温湿度稳定,这也会增加一定的生产成本。
沉金工艺与镀金工艺在成本上存在多方面的差异。企业在选择工艺时,不能仅仅依据成本来判断,还需要综合考虑产品的性能要求、生产规模、市场定位等因素。在成本控制较为重要的大规模生产项目中,如果产品对金层厚度和耐磨性要求不是特别高,沉金工艺的成本优势较为明显。而对于一些高端产品,如航空航天电子设备等,对产品性能和外观要求极高,即使镀金工艺成本高昂,企业也可能会选择该工艺以满足产品的高品质需求。只有全面权衡各种因素,企业才能做出适合自身发展的工艺选择,实现成本效益的最大化。
采购咨询,获取商机