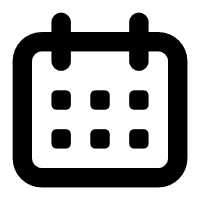
现代电子产品高速发展的趋势下,PCB的与制造面临着更高的要求。PCB背钻孔工艺作为提升信号完整性、降低信号损耗的关键技术,在高速PCB制造中发挥着重要作用。下面将详细阐述PCB背钻孔工艺流程,为相关从业者提供全面的技术参考。
PCB背钻孔,也称为控深钻孔,主要是针对过孔中不参与信号传输的多余“Stub”部分进行去除。在高速信号传输过程中,过长的过孔残桩会产生阻抗不匹配、信号反射、串扰等问题,严重影响信号质量。背钻孔工艺通过精确控制钻孔深度,将过孔残桩去除,使信号传输路径更为优化,从而有效提升信号完整性,满足高速、高频电子产品的性能需求。
资料分析与工艺规划:在进行背钻孔操作前,工程师需仔细研读PCB设计文件,明确背钻孔的位置、尺寸、深度要求等关键参数。根据PCB的层数、材料、结构等特点,制定详细的背钻孔工艺方案,包括选择合适的钻孔设备、刀具、加工参数等。
基板准备:对PCB基板进行严格检查,确保表面无污渍、划伤、变形等缺陷。同时,为了提高背钻孔的精度和稳定性,通常会对基板进行烘烤处理,去除板材中的水分,防止在钻孔过程中因水分汽化导致板材分层或爆板等问题。烘烤温度和时间需根据板材类型和供应商建议进行设置,一般烘烤温度在120℃-150℃,时间为2-4小时。
钻孔设备调试:背钻孔对设备的精度要求极高,因此需要对钻孔机进行全面调试。包括校准钻孔机的X、Y、Z轴定位精度,检查主轴的转速稳定性和跳动精度,确保设备各项性能指标符合工艺要求。此外,还需安装合适的背钻孔刀具,刀具的直径、刃长、材质等参数需根据背钻孔的尺寸和深度要求进行选择。
钻孔定位:利用钻孔机的视觉定位系统,对PCB基板上的背钻孔位置进行精确识别和定位。通过摄像头捕捉基板上的定位孔或Mark点,与设计文件中的坐标进行对比,自动调整钻孔机的工作台位置,确保钻孔位置的准确性。在定位过程中,需严格控制定位精度,一般要求定位误差在±50μm以内。
钻孔操作:启动钻孔机,按照预设的工艺参数进行背钻孔加工。在钻孔过程中,需精确控制钻孔深度,以确保能够准确去除过孔残桩。钻孔深度的控制主要通过钻孔机的Z轴伺服系统实现,同时结合深度测量装置进行实时监测和反馈调整。此外,还需合理设置钻孔速度、进给率等参数,避免因速度过快导致刀具磨损加剧、钻孔质量下降,或因速度过慢影响生产效率。一般来说,背钻孔的转速在80000-120000转/分钟,进给率在0.05-0.15mm/转。
刀具管理:由于背钻孔刀具的直径较小、刃长较短,在加工过程中容易磨损和折断。因此,需要建立完善的刀具管理系统,对刀具的使用次数、磨损情况进行实时监控。当刀具磨损达到一定程度或使用次数超过规定值时,及时更换刀具,以保证钻孔质量的稳定性。同时,对更换下来的刀具进行回收和分析,总结刀具磨损规律,优化刀具使用寿命和加工参数。
孔壁处理:背钻孔完成后,孔壁表面可能会存在毛刺、树脂残留等缺陷,需要进行孔壁处理。常见的孔壁处理方法包括化学清洗、等离子清洗等。化学清洗是通过使用化学试剂去除孔壁表面的污染物,等离子清洗则是利用等离子体的高能粒子轰击孔壁表面,达到清洁和活化的目的。通过孔壁处理,可以提高孔壁的粗糙度和清洁度,增强后续电镀层与孔壁的结合力。
电镀填孔:为了使背钻孔能够正常导通信号,需要对孔进行电镀填孔处理。首先进行孔金属化,通过化学镀铜或电镀铜的方法在孔壁表面形成一层导电铜层,然后进行电镀填孔,使孔内填满铜,形成良好的电气连接。在电镀过程中,需严格控制电镀液的成分、温度、电流密度等参数,确保电镀层的厚度均匀、致密,无空洞、气泡等缺陷。
质量检测:对完成背钻孔和电镀填孔的PCB进行全面的质量检测,主要包括外观检查、孔径测量、孔深测量、电气性能测试等。外观检查主要观察背钻孔表面是否平整、光滑,有无毛刺、划伤、分层等缺陷;孔径测量和孔深测量则使用显微镜、孔壁检测仪等设备,确保孔径和孔深符合设计要求;电气性能测试包括导通测试、绝缘电阻测试、阻抗测试等,以验证背钻孔的电气性能是否满足产品使用要求。
背钻孔深度控制是整个工艺的核心难点之一。由于钻孔深度较浅(一般在0.1-1mm之间),且精度要求高(误差要求在±25μm以内),任何微小的偏差都可能导致过孔残桩去除不彻底或损伤到正常的信号层。解决措施包括采用高精度的钻孔设备和深度测量装置,对钻孔过程进行实时监测和反馈控制;同时,通过优化钻孔参数,如降低钻孔速度、增加进给率的稳定性等,提高钻孔深度的控制精度。
在背钻孔过程中,由于刀具与板材的剧烈摩擦,容易导致孔壁表面产生毛刺、分层、树脂残留等缺陷,影响孔壁质量和电气性能。为解决这一问题,需选择合适的刀具和加工参数,减少刀具与板材的摩擦和切削力;同时,加强孔壁处理工序,采用高效的清洗和活化方法,确保孔壁表面清洁、光滑。
背钻孔工艺对设备和工艺要求较高,导致生产效率相对较低,成本增加。为提高生产效率和降低成本,可以通过优化工艺布局、采用自动化生产设备、提高刀具使用寿命等方式实现。例如,采用多轴钻孔机同时进行多个背钻孔的加工,减少设备的空闲时间;通过对刀具的优化设计和使用管理,延长刀具的使用寿命,降低刀具成本。
PCB背钻孔工艺作为高速PCB制造中的关键技术,其工艺流程涉及多个环节,每个环节都对产品质量有着重要影响。只有深入了解工艺原理,严格控制各环节的工艺参数和质量要求,不断解决工艺难点,才能确保背钻孔工艺的顺利实施,生产出高质量的PCB产品,满足现代电子产品日益增长的性能需求。
采购咨询,获取商机