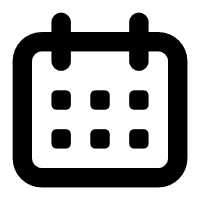
沉铜,全称化学镀铜,简称PTH。其主要目的是在PCB的非导电表面,如绝缘的孔壁及某些特定的非铜箔区域,通过化学反应沉积一层薄而均匀的铜层,赋予原本不导电的部分导电性,为后续的电镀铜工艺奠定基础,最终实现PCB的层间电气互连。
以多层PCB为例,层与层之间需要通过过孔进行电气连接。在钻孔后,孔壁是绝缘的,如果不进行沉铜处理,电流无法通过孔实现层间传导。而沉铜层就如同搭建了一座“桥梁”,使得电流能够顺畅地在各层之间流动,确保了整个电路板电气系统的完整性和功能性。若沉铜工艺出现问题,比如铜层沉积不均匀、厚度不足或存在空洞等缺陷,可能导致信号传输不稳定、短路或断路等故障,严重影响PCB的性能和使用寿命。
去毛刺:钻孔后的PCB孔口会产生毛刺,孔内可能残留钻屑。通过机械刷磨等方式去除这些毛刺和钻屑,保证后续处理的顺利进行,避免对孔壁和板面造成损伤,影响沉铜效果。
溶胀:对于多层板,其内层的环氧树脂在钻孔过程中可能被破坏。使用特定的溶胀剂,如醚类有机物,使环氧树脂溶胀软化,为后续的去钻污步骤做准备,确保能有效去除钻污,增强孔壁与铜层的结合力。
除胶去钻污:利用高锰酸钾的强氧化性,在高温及强碱条件下,与溶胀软化的环氧树脂钻污发生氧化裂解反应,将其去除。例如,在一定温度和碱性环境下,高锰酸钾与环氧树脂中的碳链反应,使其断裂分解,从而达到清洁孔壁的目的。
中和:除去高锰酸钾去钻污过程中残留的高锰酸钾、锰酸钾和二氧化锰等物质。因为锰离子属于重金属离子,会导致后续活化步骤中“钯中毒”,使钯离子或原子失去活化活性,进而影响孔金属化的效果,所以必须彻底去除。
除油/整孔:采用专用的除油剂,清除板面的油污及其他杂质。同时,通过整孔剂的作用,调整孔壁的电荷性质,使其表面显正电性,促进后续均匀的催化剂吸附。
微蚀:使用微蚀液除去铜面上的氧化物及其他杂质,微观粗化铜表面。这不仅能增强铜面与后续电解铜的结合能力,还能为催化剂的吸附提供更合适的表面环境。
浸酸:对微蚀后铜面上附着的铜粉进行清洁,确保铜表面的纯净度,为后续的活化步骤创造良好条件。
催化
预浸:防止前工序清洗不彻底,杂质带入昂贵的钯槽,同时润湿环氧树脂孔壁,促进板面对催化剂的吸附。预浸槽与后续的活化槽除了不含钯之外,其他成分基本一致。
活化:这一步通常使用Pd/Sn或Pd/Cu等催化剂,使表面显负电性的钯胶团由于整孔性高分子的作用附着在孔壁。通过活化处理,为后续的化学沉铜提供催化活性中心,使铜离子能够在这些活性点上发生还原反应。
加速:去除胶体钯微粒外层的胶体部分,露出起催化作用的钯核,保证化学镀铜层与孔壁有良好的结合力。例如,钯胶团粘附在板子上,经水洗和鼓气作用,Pd粒外会形成Sn(OH)4外壳,通过HBF4型加速剂将其除去,露出钯核。
化学沉铜:将经过催化处理的PCB放入含有铜盐(如硫酸铜)和还原剂(如甲醛)的化学沉铜槽中。在钯核的催化作用下,铜离子被甲醛还原,沉积在PCB的孔壁和需要导电的非铜箔表面,逐渐形成一层薄铜层。随着反应的进行,新生成的化学铜和反应副产物氢气都可以作为反应催化剂,进一步促进反应的持续进行,使铜层不断增厚。化学沉铜的类型根据需求可分为薄铜(0.25-0.5μm)、中铜(1-1.5μm)及厚铜(2-2.5μm)。
水洗:沉铜完成后,通过多级水洗,彻底去除PCB表面残留的化学药品,防止残留物质对后续工序产生不良影响。
干燥:采用热风烘干等方式,去除PCB表面的水分,使其处于干燥状态,便于后续的存储和加工。
质量检测
背光等级测试:制作孔壁切片,使用金相显微镜观察沉积铜在孔壁的覆盖情况。背光等级一般分为10级,等级越高,沉积铜在孔壁的覆盖情况越好。通常情况下,行业标准要求≥8.5级。通过背光等级测试,可以直观地了解沉铜层在孔壁的均匀性和完整性,判断沉铜质量是否符合要求。
铜层厚度检测:使用X射线测厚仪等专业设备,测量沉铜层的厚度,确保其达到设计要求的厚度范围。不同的应用场景和产品要求,对沉铜层厚度的标准有所差异。
附着力检测:通过胶带测试等方法,检测铜层与PCB基材之间的附着力。例如,使用特定粘性的胶带粘贴在沉铜层表面,然后迅速撕下,观察铜层是否有脱落现象,以此评估附着力是否达标。良好的附着力是保证沉铜层稳定性和可靠性的重要指标。
孔壁检查:利用显微镜等工具,仔细检查孔壁的铜层是否连续、有无空洞、裂纹等缺陷,确保孔壁的铜层质量满足电路可靠性的要求。
温度控制:化学沉铜过程中的反应速率对温度非常敏感。温度过高,反应速度过快,可能导致铜层沉积不均匀,出现粗糙、空洞等缺陷;温度过低,反应速率慢,沉铜效率低,且铜层厚度难以达到要求。例如,化学沉铜槽的温度一般需精确控制在25-35℃之间,具体温度根据所使用的化学药水配方和工艺要求而定。
pH值控制:溶液的pH值会影响铜离子的存在形式和还原剂的活性。不合适的pH值会使反应无法正常进行,或者导致铜层质量下降。在沉铜过程中,通常需要将pH值控制在11-13的碱性范围内,通过添加pH调节剂来维持稳定的pH值。
药水浓度控制:铜盐、还原剂、络合剂等药水成分的浓度必须严格控制在规定范围内。浓度过高或过低都会影响沉铜的速率和质量。例如,铜盐浓度过低,会导致沉铜速度慢,铜层厚度不足;还原剂浓度过高,可能引起反应过于剧烈,影响铜层的均匀性。需要定期对药水浓度进行检测和调整,确保其处于最佳工艺状态。
反应时间控制:沉铜时间决定了铜层的最终厚度。时间过短,铜层厚度达不到设计要求;时间过长,不仅浪费资源,还可能导致铜层过厚,出现结晶粗大、附着力下降等问题。根据不同的沉铜类型和工艺要求,精确控制沉铜时间,如薄铜沉铜时间一般在10-15分钟,中铜和厚铜则相应延长。
电子技术的不断进步,使得对PCB的要求越来越高,如线路更加精细、孔径更小、层数更多、性能更可靠等,这也推动着沉铜工艺不断发展创新。一方面,研发新型的活化剂和还原剂,以提高沉铜速率、改善铜层质量,同时降低成本和减少环境污染;另一方面,利用更先进的自动化控制设备,实现对沉铜工艺参数的精准控制,提高生产过程的稳定性和一致性。此外,为适应环保要求,无铅、无氰等绿色沉铜工艺也成为研究和发展的重点方向。
采购咨询,获取商机