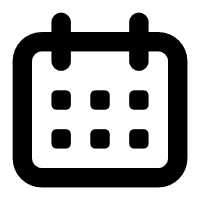
PCB作为电子产品的核心部件,其性能与质量直接关乎整个电子设备的稳定性和可靠性。而在影响PCB性能的诸多因素中,抗氧化能力占据着举足轻重的地位。
PCB主要由导电线路、绝缘基材以及各类电子元件构成。在日常使用时,PCB会遭遇多种环境因素的挑战,氧化便是一个不容忽视的问题。空气中的氧气、水分以及各类污染物,都可能与PCB上的金属线路发生化学反应,致使线路腐蚀、电阻增大、信号传输不稳定,甚至引发电路故障。尤其是PCB上的铜箔线路和焊点等金属部分,在空气中极易与氧气发生反应,生成氧化物。这些氧化物会增大线路电阻,干扰信号传输的稳定性,严重时还会造成线路断路,致使电子设备无法正常工作。
这是一种较为常用的PCB抗氧化工艺,通过在PCB表面生成一层薄薄的有机保护膜,将金属与空气隔离,从而发挥抗氧化功效。其原理基于化学键合,以常见的唑类OSP为例,烷基苯并咪唑类有机化合物中的咪唑环能与铜原子的3d10电子形成配位键,进而形成烷基苯并咪唑-铜络合物。在涂覆过程中,先涂覆第一层,该层会吸附铜,接着第二层有机涂覆分子与铜结合,如此反复,直至形成由许多次有机涂覆分子集结的结构,最终在铜表面形成厚度一般在0.2-0.5µm之间的保护层。并且,由于长链烷基之间通过范德华力相互吸引,加上苯环的存在,这层保护膜具备良好的耐热性和较高的分解温度。在后续的焊接高温环境中,这种保护膜又能够很容易地被助焊剂迅速清除,使露出的干净铜表面能在极短时间内与熔融焊锡结合,形成牢固的焊点。
OSP工艺成本相对较低,工艺过程不复杂,适合大规模生产。而且能良好保持焊盘可焊性,保障焊接质量。但它也存在一些缺点,比如膜层薄导致存储时间有限,抗氧化性能易随时间和环境变化而下降;不耐高温,在需多次高温制程的场景中受限;对焊接环境要求严苛,环境中的杂质、湿度等因素易影响其性能和焊接质量。
该工艺是在PCB表面先镀上一层镍,再镀上一层金。镍层能够阻挡铜的扩散,金层则具备良好的抗氧化性和导电性,能显著提升PCB的性能和可靠性。化学镀镍金工艺成熟,货源充足,适用于无铅焊接。然而,该工艺成本相对较高,且其表面不够平整,在焊接细间距元件时存在困难。
浸银工艺能在PCB表面形成一层均匀的银层,具有良好的抗氧化性和可焊性。银层下面没有镍层,所以浸银在物理强度方面不如化学镀镍/浸金。银层暴露在空气中会经历双重腐蚀路径,化学氧化下,4Ag+O₂→2Ag₂O,生成黄色氧化层;电化学腐蚀中,Ag+H₂S→Ag₂S+H₂,产生黑色硫化物。当相对湿度>60%时,腐蚀速率提高3倍;在含硫环境中,如橡胶包装,24小时即可出现可见变色。
浸锡
浸锡工艺使PCB表面覆盖一层锡,可有效防止氧化。由于所有焊料都以锡为基础,锡层能与任何类型的焊料匹配。不过,过去浸锡工艺处理的PCB易出现锡须问题,在焊接过程中,锡须和锡迁移现象会给可靠性带来严重挑战。后来,通过在浸锡溶液中添加有机添加剂,使锡层结构转变为颗粒状,克服了上述难题,并且具备良好的热稳定性和可焊性。浸锡板的存储时间有限,放置过久其表面会形成氧化锡,从而影响焊接效果,因此在组装时必须严格按照浸锡的先后顺序进行操作。
热风整平,又称热风焊料整平,俗称喷锡。该工艺是在PCB表面涂覆熔融的锡铅焊料如今更多使用无铅焊料,然后利用加热压缩空气将焊料整平,从而形成一层既能有效抵抗铜氧化,又能提供优良可焊性的涂覆层。在热风整平时,焊料与铜相互作用,在结合处生成铜锡金属化合物。该工艺分为垂直式和水平式,水平式因镀层更为均匀,且能实现自动化生产,而被普遍认为更具优势。其一般流程包括微蚀、预热、涂覆助焊剂、喷锡、清洗等步骤。热风整平工艺成熟,成本相对较低,且具有良好的可焊性,适用于无铅焊接。但其表面不够平整,在焊接细间距元件时存在困难,并且含铅的HASL还面临环保问题。
在多层PCB制造过程中,内层铜箔表面的处理对层压质量至关重要,棕化工艺在其中应用广泛。其核心是通过化学氧化反应,在铜表面形成一层多孔的氧化铜或氧化亚铜膜。在碱性氧化剂作用下,铜发生氧化反应,2Cu+4OH⁻+O₂→2CuO+2H₂O,Cu+2OH⁻→Cu₂O+H₂O+2e⁻。棕化不仅能提供良好的层间结合力,还能提高层压过程中树脂的润湿性。棕化层的多孔结构增加了铜箔表面积,利于树脂渗透填充微孔,减少层压时气泡和空洞,增强机械咬合力,减少分层风险。在PCB热循环中,还能更均匀分布应力,降低层间剥离风险,提高热可靠性。不过,若控制不当,过度氧化会使氧化层过厚变脆,降低结合强度;氧化不均会导致结合力不一致,增加分层风险;棕化在后续层压前若受污染,如吸湿或氧化膜受损,也会导致结合力下降。通常氧化层厚度控制在0.5-1.5μm之间,在进行棕化之前,会采用微蚀工艺去除铜表面的氧化物和有机污染物,常见微蚀剂包括过硫酸铵或硫酸-过氧化氢体系。棕化溶液通常由碱性氧化剂、络合剂和稳定剂组成,通过调整氧化条件,可获得最优的CuO/Cu₂O比例,以兼顾结合力和耐热性。棕化后的铜表面容易受湿气或空气污染,在层压前通常需要进行抗氧化处理,如使用有机保护层,如苯并三氮唑或其他防氧化剂,以及进行干燥存储,避免湿气吸收,减少变质风险。
在PCB的制造过程中,选用高质量的基材和金属材料至关重要。优质的基材具备良好的绝缘性能和稳定性,能够有效阻隔氧气和水分的侵入。同时,采用抗氧化性能强的金属镀层,如镀金、镀银、镀锡等,可以在金属线路表面形成一层保护膜,阻止氧化反应的发生。例如,在一些高端电子产品中,会选用抗氧化性能出色的无氧铜箔作为覆铜箔材料,以提升PCB的整体抗氧化能力。
合理的存储和使用环境对PCB的抗氧化同样关键。在PCB的生产、储存和运输过程中,应严格控制环境的温度和湿度,避免PCB暴露于高温高湿或含有污染物的环境中。例如,将PCB存储在相对湿度控制在40%-60%,温度控制在20℃-25℃的环境中,可有效减缓氧化速度。同时,选择合适的包装材料,如防潮袋、泡沫箱等,确保PCB的完整性和质量。对于暂时不进行后续组装的裸板,采用真空包装可以有效隔绝空气,延缓氧化过程。
生产流程优化
优化生产流程,减少PCB在制程间暴露于空气中的时间,也能降低氧化风险。例如,通过自动化设备快速完成从蚀刻到阻焊的转换,避免不必要的等待时间。在PCB制造的特定阶段使用抗氧化剂溶液对铜面进行处理,可以在短时间内为铜面提供临时保护,直到下一道工序开始前。
PCB抗氧化对于保障电子设备的稳定运行和延长使用寿命意义重大。在电子技术的持续发展,对PCB的抗氧化要求也会越来越高,这也就意味着需要从制造、工艺、存储和使用等多个环节共同发力,不断研发和创新,以提升PCB的抗氧化性能,为电子设备的高性能和高可靠性提供有力支撑。
采购咨询,获取商机