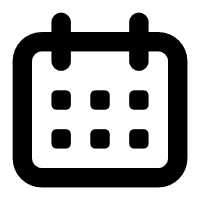
PCB塞孔工艺是确保电路板性能与可靠性的关键环节,随着电子产品朝着“轻、薄、短、小”方向发展,PCB的集成度不断提高,塞孔工艺的重要性愈发凸显。以下将详细介绍PCB塞孔的工艺流程。
在正式开始塞孔流程前,需进行一系列准备工作。首先,要确保待加工的PCB板表面清洁,无油污、灰尘及其他杂质,以免影响塞孔效果。可采用超声波清洗、化学清洗等方式对PCB板进行预处理,随后进行烘干,保证板面干燥。其次,根据PCB板的设计要求,选择合适的塞孔材料,常见的有树脂、油墨等。不同材料适用于不同的应用场景,例如,对于有较高电气性能要求的场合,会选用具有良好绝缘性和稳定性的树脂材料;而对于一般的阻焊塞孔需求,热固性或感光性油墨较为常用。同时,还需准备好塞孔所需的设备,如丝印机、塞孔机等,并对设备进行调试,确保其参数设置符合工艺要求,如丝印机的网版张力、刮刀压力、印刷速度等,塞孔机的注胶压力、流量等。
钻孔是PCB制造的前期工序,但与塞孔紧密相关。根据电路设计,使用数控钻床在PCB板上钻出导通孔或盲孔。钻孔的精度、孔径大小及孔壁质量会直接影响后续塞孔效果。为保证钻孔质量,需选择合适的钻头,并控制好钻孔参数,如转速、进给量等。例如,对于较薄的PCB板,可适当提高转速、降低进给量,以减少孔壁的毛刺和粗糙度;而对于较厚的PCB板,则需调整参数,确保钻孔的垂直度和贯通性。钻完孔后,要对PCB板进行检查,去除孔内残留的钻屑等杂质,为后续塞孔做准备。
孔壁处理的目的是提高塞孔材料与孔壁的附着力,确保塞孔的牢固性。一般采用化学处理方法,如对孔壁进行微蚀处理,通过特定的化学溶液去除孔壁表面的氧化层、油污等,使孔壁呈现微观粗糙状态,增加塞孔材料与孔壁的接触面积。在微蚀过程中,要严格控制溶液浓度、处理时间和温度等参数。处理完成后,需用清水对PCB板进行充分冲洗,去除残留的化学溶液,再进行烘干处理,保证孔壁干燥。对于一些特殊要求的PCB板,可能还需在孔壁上进行化学镀铜等预处理,进一步增强孔壁与塞孔材料的结合力。
塞孔是整个工艺流程的核心步骤。目前常见的塞孔方式有树脂塞孔和油墨塞孔。
手工填胶:对于少量、特殊规格的PCB板,可采用手工填胶方式。使用专用的注射器或工具,将调配好的树脂材料缓慢注入孔内,确保树脂填充饱满,无气泡残留。在填充过程中,需注意控制填充速度和力度,避免树脂溢出孔外过多。填充完成后,用工具将孔口多余的树脂刮平。
真空塞孔:对于大规模生产且对塞孔质量要求较高的情况,常采用真空塞孔设备。将PCB板放置在真空环境中,通过设备将树脂材料注入孔内。在真空状态下,孔内的空气被抽出,有利于树脂更充分地填充到孔的各个角落,减少气泡产生,提高塞孔的密实度。例如,一些高端电子产品的PCB板制造,会优先选择真空塞孔工艺,以保证产品的可靠性。
印刷塞孔:利用丝印机进行塞孔操作。将带有对应孔位图案的网版安装在丝印机上,通过刮刀将树脂材料刮过网版,使树脂填充到PCB板的孔中。这种方式适用于孔径较大、数量较多且分布规则的孔。在丝印过程中,要调整好丝印参数,如刮刀压力、网版与PCB板的间距等,确保树脂填充均匀、饱满。
铝片网版塞孔:使用数控钻床在铝片上钻出与PCB板塞孔位置对应的孔,制成铝片网版。将铝片网版安装在丝印机上,采用热固性或感光性油墨进行塞孔。在丝印过程中,油墨通过铝片网版上的孔填充到PCB板的导通孔内。此方法能较好地控制油墨填充量,保证塞孔的一致性,但对铝片网版的制作精度要求较高。
直接丝印塞孔:采用特定目数的丝网,如36T或43T丝网,安装在丝印机上,在完成板面阻焊油墨印刷的同时,将导通孔塞住。这种方式工艺流程相对简单,但由于过孔内存有大量空气,在后续固化过程中,空气膨胀可能会冲破阻焊膜,造成空洞、不平整等问题,因此对油墨的性能和丝印参数的控制要求较为严格。
塞孔完成后,需对填充的树脂或油墨进行固化处理,使其具有一定的强度和稳定性。
热固化:将塞孔后的PCB板放入烘箱中,根据树脂材料的特性,设置合适的温度和时间进行加热固化。一般热固化温度在120℃-180℃之间,时间为30-90分钟不等。在固化过程中,树脂分子发生交联反应,形成三维网状结构,从而提高树脂的硬度和强度。例如,对于一些环氧树脂类塞孔材料,常采用150℃下固化60分钟的工艺参数。
光固化:若使用的是光固化树脂,可通过紫外线照射进行固化。将PCB板放置在紫外线固化设备中,根据树脂对紫外线波长的敏感特性,选择合适的光源和照射时间。光固化速度快,生产效率高,且能减少热对PCB板的影响,适用于对热敏感的PCB板或对生产效率要求较高的场景。
热固性油墨固化:与树脂热固化类似,将塞孔后的PCB板放入烘箱,在特定温度下使油墨中的树脂成分发生交联固化。热固性油墨的固化温度一般在150℃-200℃,时间为20-60分钟。不同品牌和型号的热固性油墨,其固化参数会有所差异,需根据实际情况进行调整。
感光性油墨固化:先对塞孔后的PCB板进行预烘,去除油墨中的溶剂,使油墨初步干燥。然后进行曝光,通过紫外线照射,使油墨中的感光成分发生光化学反应,形成交联结构。最后进行显影,去除未曝光部分的油墨,留下固化的塞孔油墨。曝光时间和显影参数需根据油墨的感光特性和PCB板的具体要求进行精确控制。
固化后的塞孔表面可能存在不平整的情况,需要进行打磨处理,使PCB板表面平整光滑,满足后续工艺要求。
机械打磨:采用磨板机等设备,通过砂纸或砂轮等打磨工具对PCB板表面进行打磨。在打磨过程中,要控制好打磨压力、速度和时间,避免过度打磨导致塞孔材料被磨穿或PCB板表面受损。打磨后,需对PCB板进行清洗,去除表面残留的粉尘等杂质。
化学抛光:对于一些对表面平整度要求极高的PCB板,可采用化学抛光方法。将PCB板浸泡在特定的化学溶液中,通过化学反应去除表面的微小凸起,使表面达到平整光滑的效果。化学抛光能在不损伤PCB板内部电路的情况下,有效提高表面质量,但需要严格控制化学溶液的浓度、温度和处理时间等参数。
经过以上完整的塞孔工艺流程,PCB板的导通孔或盲孔被有效填充,从而满足电子产品在电气性能、焊接工艺等方面的要求,为后续的电子元件安装和整机组装奠定良好基础。
采购咨询,获取商机