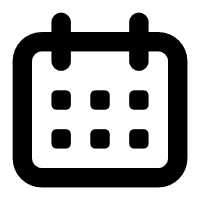
现代电子设备中,无论是微小的智能手表,还是复杂的超级计算机,PCB都承载着电子元器件的电气连接,是电子产品实现功能的关键所在。其制作流程复杂且精密,涉及众多工艺环节,每个步骤都对最终产品的性能和质量起着决定性作用。
依据设计要求,挑选适配的覆铜板。覆铜板由铜箔、绝缘基材构成,常见的绝缘基材有玻璃纤维环氧树脂、聚酰亚胺等。不同基材具备不同电气、机械与热性能,FR-4适用于多数普通电子产品,而PI在高温、高频等特殊应用场景中表现更为出色。同时,要确定覆铜板的铜箔厚度,常见厚度有18μm、35μm、70μm等,依据线路板的电流承载能力、信号传输要求等因素抉择。
运用切割设备,如数控切割机,将大尺寸覆铜板切割成契合后续生产加工的小块。切割时,尺寸精度要求严苛,误差通常控制在极小范围,如±0.1mm,以契合设计要求。同时,注重切割平整度,防止板材边缘出现毛刺或不平整状况,以免对后续加工工序造成影响。
开料后的覆铜板,先进行表面清洁与粗化处理。清洁旨在去除板材表面的油污、灰尘等杂质,可采用化学清洗剂与物理刷洗相结合的方式。粗化处理则借助化学蚀刻或机械研磨等手段,让板材表面粗糙化,增强后续压膜时干膜与板材表面的附着力。之后,进行微蚀处理,进一步清除表面氧化层,使铜表面活化,微蚀量一般控制在1-2μm左右。
将干膜通过热压贴合到处理后的覆铜板表面。压膜的温度、压力和速度等参数,需依据干膜特性与板材状况进行调整,一般压膜温度在100-120°C,压力在3-5kg/cm²左右,速度在1-2m/min左右。接着,把压膜后的覆铜板置于曝光机下,按照Gerber文件中的内层线路图形,经紫外光照射使干膜曝光。曝光能量要精准把控,过高会致使干膜过度曝光、图形变形,过低则会使干膜曝光不充分、图形模糊,曝光能量通常依据干膜类型和厚度在80-150mJ/cm²之间调节。随后,使用显影液溶解去除未曝光的干膜,留存曝光后的干膜图形,达成将Gerber文件中的内层线路图形转移到覆铜板上的目的。显影液的浓度、温度和显影时间都需严格控制,例如显影液浓度一般在1%-3%左右,温度在30-35°C,显影时间在60-90s左右。
把显影后的覆铜板放入蚀刻液中,蚀刻液会腐蚀掉未被干膜保护的铜箔,进而形成内层线路。蚀刻液多采用酸性蚀刻液,如氯化铜蚀刻液,蚀刻过程中要对蚀刻液的浓度、温度、蚀刻速度等参数加以控制。蚀刻液浓度一般在1-2mol/L左右,温度在40-50°C,蚀刻速度依据线路密度和蚀刻设备的不同在1-3μm/min左右。蚀刻结束后,对蚀刻后的覆铜板进行清洗,去除残留蚀刻液和铜离子。最后,运用自动光学检测设备对内层线路展开检测。AOI设备通过光学成像和图像分析技术,检查线路是否存在开路、短路、线宽不符等缺陷,一旦发现差异超出设定阈值,便会标记为缺陷点。
对内层线路板进行棕化处理,在铜表面生成一层均匀、具有一定粗糙度和化学活性的棕化膜。棕化过程中,棕化液与铜表面发生化学反应,棕化膜厚度一般在0.5-1.5μm左右。棕化膜能够提升内层线路与半固化片之间的结合力,有效防止分层现象的发生。
依据设计层数,将经过棕化处理的内层线路板、半固化片按特定顺序叠合。叠合时,务必确保各层定位精准,误差控制在极小范围,如±0.05mm。半固化片在压合过程中,会将各层线路板粘结在一起,并填充层间空隙。之后,把叠合好的多层板放入压合机中进行压合。压合机通过高温和高压作用,使半固化片熔化并流动,将各层线路板牢固粘结,形成多层板结构。压合过程中的温度、压力和压合时间等参数,需依据板材类型、层数和半固化片特性等因素精确调节,压合时间一般在60-120min左右。
压合后的多层板要进行后处理,去除板边多余材料,如溢胶等,并对板边进行打磨和倒角处理,提升多层板的外观质量与机械性能。
根据Gerber文件中的过孔信息,对钻孔设备进行编程,确定每个过孔的坐标位置、孔径大小、钻孔顺序等信息。编程时,要兼顾钻孔效率与质量,优化钻孔顺序,减少钻孔设备的空行程时间。
使用数控钻孔机依照编程设定参数进行钻孔。钻孔时,要严格控制钻孔速度、进给量和钻头转速等参数。对于不同直径的钻头和不同板材材料,这些参数需相应调整。例如,直径较小的钻头,如0.2mm,钻孔速度应适当降低,防止钻头折断;对于较硬的板材材料,钻头转速可能要提高。钻孔过程中,要保证孔径精度,误差通常控制在±0.05mm以内,同时注重钻孔垂直度,避免出现斜孔,因为斜孔会影响后续孔金属化和电气连接质量。钻孔完成后,对孔壁进行清洁处理,去除钻孔过程中产生的碎屑、油污等杂质,可采用高压空气吹洗、化学清洗等方式,确保孔壁清洁、干燥,为后续孔金属化做好准备。
先对孔壁进行活化处理,使孔壁铜表面活化,便于后续化学镀铜顺利进行。活化处理一般采用钯盐溶液,通过化学反应在孔壁铜表面吸附一层钯原子,作为化学镀铜的催化中心。活化过程中,要控制活化液的浓度、温度和处理时间,活化液浓度一般在0.1-0.3g/L左右,温度在30-40°C,处理时间在3-5min左右。
在活化后的孔壁上进行化学镀铜。化学镀铜溶液含有铜盐、还原剂等成分,在钯原子催化作用下,铜离子在孔壁被还原成铜原子,从而在孔壁形成一层薄铜层。化学镀铜过程中,要严格控制镀液的浓度、温度、pH值和镀覆时间等参数,镀液浓度一般为硫酸铜10-20g/L、甲醛5-10g/L,温度在25-35°C。化学镀铜形成的铜层较薄,为满足电气性能要求,还需进行电镀加厚。电镀时,在线路图形裸露的铜皮上或孔壁上电镀一层达到规定厚度的铜层,以及根据需求电镀金、镍或锡层等。电镀过程同样要精确控制电镀液的成分、浓度、温度、电流密度等参数,以确保镀层厚度均匀、性能优良。
与内层类似,先对外层表面进行清洁处理,去除污染物。接着进行压膜、曝光、显影操作,将设计好的外层线路图案转移到板上。压膜、曝光、显影的工艺参数控制与内层线路制作相近,但由于外层线路制作更为复杂,对精度要求更高,因此各参数的控制精度也更为严格。
在曝光显影后的线路图案上进行图形电镀,加厚线路。电镀完成后,去除干膜,再用蚀刻液蚀刻掉未被保护的铜层,形成最终的外层线路。之后,根据需要进行剥锡等后续处理,使线路达到设计要求的状态。
在板子上涂覆一层感光阻焊油墨,通过曝光显影形成阻焊层,保护线路不被误焊接。同时,进行表面处理,如化学镍金处理,提高焊接性能和耐腐蚀性。化学镍金处理过程中,先镀镍再镀金,镍层可阻挡铜的扩散,金层具有良好的抗氧化性和导电性,能显著提升PCB的性能和可靠性。
在板子上印刷文字、标记符号,方便后续组装和维修,为电子产品的生产、调试和维护提供便利。
检测合格后,对PCB板进行真空包装、打包发货,确保产品在运输过程中不受损坏,顺利交付给客户。
PCB线路板的制作工艺流程是一个环环相扣、精密复杂的过程,每一个环节都凝聚着技术人员的智慧与心血,只有对每个工艺步骤进行严格把控,才能制造出高质量的PCB板,为现代电子设备的稳定运行提供坚实保障。
采购咨询,获取商机