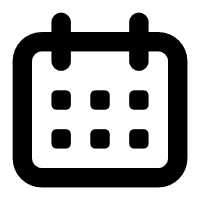
电子产品的核心架构中,PCB如同精密运作的“神经中枢”,其性能优劣直接决定着电子产品的稳定性与可靠性。而压合工艺作为PCB制造流程中的核心环节,肩负着将多层材料融合为稳定结构的重任,其工艺精度不仅影响PCB的机械强度、绝缘性能,更对信号传输的完整性起着决定性作用。下面将系统解析PCB压合工艺的全流程,揭示其背后的技术逻辑与质量控制要点。
内层芯板作为PCB的电气连接基础,需经历内层线路制作的精密加工,确保线路图形的精度误差控制在±5μm以内。在外观检测环节,采用自动光学检测设备对芯板进行全表面扫描,重点排查线路短路、断路及直径大于50μm的针孔缺陷,同时通过微电阻测试仪对线路导通性进行100%测试,确保芯板电气性能达标。
半固化片的性能参数直接决定层间结合质量。针对高频通信类PCB,需选用介电常数≤3.0、介质损耗≤0.002的低损耗型半固化片;而对于汽车电子等高可靠性场景,则需采用玻璃化转变温度≥170℃的耐高温型号。在材料入库检验中,通过凝胶时间测试仪检测树脂固化活性,要求凝胶时间偏差控制在±10%以内,同时利用厚度测量仪对片材均匀性进行抽检,确保厚度公差≤±5μm。
外层铜箔的选择需匹配电路设计需求。对于大电流场景,如电源模块,优先选用70μm厚度的高延展性铜箔,其抗剥离强度需≥1.5N/mm;而高频信号线路则宜采用18μm的超低轮廓铜箔,以降低趋肤效应影响。铜箔表面粗糙度需控制在1.5-2.5μm范围内,通过粗糙度测量仪进行批次抽检,杜绝因表面缺陷导致的蚀刻不良问题。
叠层设计需遵循电磁兼容原则,对于10层以上的高速PCB,通常采用“信号层-地层-电源层-信号层”的对称结构,电源层与地层间距控制在50-100μm,以形成紧密耦合的电容效应,降低电源噪声。在盲埋孔设计中,通过CAE软件进行孔位投影分析,确保相邻层盲孔偏差≤50μm,避免因错位导致的层间连接失效。典型案例显示,采用6层对称叠层的DDR4电路板,其信号完整性仿真损耗较非对称结构降低12%。
叠放操作在千级洁净室环境下进行,操作人员需佩戴防静电手套及口罩,避免人体污染物影响。采用视觉对位系统对各层材料进行定位,X/Y轴对位精度可达±25μm。辅助材料方面,选用耐高温聚酰亚胺隔离纸(耐温≥260℃),其厚度公差控制在±2μm,缓冲材料采用密度0.3g/cm³的玻璃纤维毡,以均衡压力分布。叠层完成后,需通过称重法对材料总厚度进行验证,误差需≤±3%。
温度控制采用多区温控技术,压合钢板表面温差≤±1.5℃。以某FR-4材料为例,其固化曲线分为三个阶段:预热段(60-120℃,升温速率3℃/min)、固化段(180℃±2℃,保温90min)、后固化段(逐步降温至80℃以下)。通过红外测温仪实时监测板坯中心温度,确保与设定曲线偏差≤±3℃。
压力调控采用伺服液压系统,压力梯度控制在5psi/mm以内。对于8层PCB,初始压力设定为150psi,当温度升至120℃时(树脂熔融阶段),逐步升压至400psi,保压阶段压力波动≤±10psi。大面积板件(≥400mm×500mm)需启用分区压力补偿功能,通过压力传感器矩阵实现局部压力动态调整,确保板厚均匀性误差≤±5μm。
时间管理遵循“温度-压力-时间”三维协同原则。实验数据表明,在180℃/400psi条件下,半固化片完全固化需85-95min,低于80min则层间剥离强度下降20%以上。对于厚铜箔(≥70μm)工艺,需延长保压时间15-20min,以确保树脂充分填充铜箔凹陷处。
升温阶段通过PLC系统记录每分钟温度变化,当升温速率超过5℃/min时自动触发警报。此阶段重点观察树脂熔融状态,理想情况下,半固化片在90-110℃区间开始呈现流态,若出现提前熔融(如80℃以下),需排查材料存储环境(湿度需≤5%RH)。
保温保压阶段利用压力变送器实时监测油缸压力,当压力波动超过±15psi时,系统自动启动补偿泵进行压力修正。同时通过安装在钢板内的热电偶传感器,每5min记录一次温度数据,形成温度-时间曲线,用于工艺追溯与优化。
冷却阶段采用梯度冷却工艺,先在设备内自然冷却至120℃以下(冷却速率≤5℃/min),再转移至风冷隧道(风速2-3m/s)冷却至室温。对于高TG材料(Tg≥180℃),需在80℃以上保持缓冷30min,以减少内应力积累,经测试,该工艺可使PCB翘曲度降低40%以上。
目视检测采用多角度光源照明(色温5000-6500K),检测人员需具备2年以上经验,可识别直径≥0.3mm的气泡、长度≥1mm的分层缺陷。对于边缘溢胶,采用激光测厚仪检测溢胶厚度,要求≤0.1mm,避免影响后续铣边精度。
显微镜检查使用50-200倍光学显微镜,重点观察盲埋孔连接处的树脂填充情况,要求空洞率≤5%。对于高密度线路区域,通过切片分析检查层间对准度,X/Y轴偏移需≤50μm,Z轴树脂厚度均匀性误差≤±10%。
尺寸测量采用影像测量仪,对板件长宽尺寸、孔径位置进行全自动扫描,坐标精度达±10μm。对于异形板件,通过CAD数据导入实现轮廓匹配,尺寸公差控制在±0.05mm以内。
厚度检测使用千分尺对板件四角及中心共5点进行测量,平均厚度与设计值偏差≤±3%,各测点厚度极差≤50μm。对于多层板,通过X射线测厚仪非破坏性检测各层铜厚,要求内层铜厚偏差≤±10%,外层铜厚偏差≤±5%。
缺陷修复对于面积≤5mm²的气泡,采用真空热压修复技术(温度180℃、压力600psi、时间10min),修复后需重新进行切片验证;对于线路微短路,使用激光微蚀设备(光斑直径≤50μm)精准去除短路点,修复后通过飞针测试确认导通性。统计显示,轻微缺陷修复成功率可达90%以上,但修复次数限制为≤2次。
报废处理建立严格的缺陷分级标准,凡涉及以下情况之一者判定为报废:①层间分离面积>100mm²;②关键信号网络断路/短路;③翘曲度>1.5%;④孔径偏差>±100μm。报废品需进行粉碎处理,并通过ERP系统记录报废原因,以便工艺改进追溯。
PCB压合工艺是集材料科学、热压传递、精密控制于一体的复杂制造过程,其技术要点贯穿“材料准备-叠层设计-压合执行-检测修复”全链条。通过精准的材料选型、科学的叠层规划、智能的设备控制及严格的质量检测,可有效提升PCB的综合性能指标。
采购咨询,获取商机