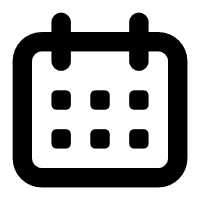
新能源汽车飞速发展使得电子系统的复杂程度与性能要求达到了全新的高度。多层PCB板凭借其出色的电气性能、高集成度和可靠性,成为众多关键设备的核心组成部分,深度嵌入新能源汽车的动力、智能、安全等各个系统。
BMS堪称电池包的“大脑”,对电池的充放电、温度、均衡等进行全方位管控,其核心硬件便是多层PCB板。新能源汽车的电池组由大量单体电池串联、并联组成,BMS需实时、精准地监测每个电芯的电压、电流和温度等参数。以特斯拉Model3的BMS为例,其采用8层板设计,阻抗公差严格控制在±5%以内,以此保障信号完整性。因为BMS要处理如电压采样、电流检测以及CAN通信等敏感信号,多层PCB板拥有专属信号层,可将信号线与电源线、地线分离,避免干扰,确保ADC采样值稳定、高频噪声得到有效抑制,CAN总线通信顺畅,防止BMS误报故障。同时,在散热方面,多层PCB板的中间层可采用大面积电源铜皮均匀散热,底层地平面充当“散热板”,配合过孔将芯片热量导出,避免芯片因过热降频,确保BMS在电池包高温环境下稳定运行。
MCU负责控制驱动电机的运转,接收整车控制器指令,精确调节电机的速度与扭矩。在这一过程中,它需承载高电压的瞬时电流冲击,对PCB板的电气性能和散热能力要求极高。传统的FR-4基材难以胜任,多层PCB板则通过采用陶瓷基覆铜板等新型材料,将热导率提升至8W/m・K,可支持120℃以上长期稳定运行,有效解决因局部过热导致的性能衰减问题。此外,多层PCB板还能凭借其多层结构,合理布局功率电子元件,如电机驱动器和逆变器等,实现高效的功率转换和精准的电机控制,保障车辆动力输出的平稳性与高效性。
该系统为驾乘人员提供音频、视频播放,导航以及车辆信息显示等丰富功能,多层PCB板在其中发挥着关键作用。一方面,它要连接显示屏与控制芯片、各类传感器,实现仪表盘数据的实时、清晰呈现以及人机交互操作的流畅响应;另一方面,随着智能座舱技术的发展,系统需集成更多功能,如手势识别、语音控制等,这就要求多层PCB板具备更高的集成度和信号传输能力。多层PCB板通过高密度布线和小型化设计,能够在有限空间内满足复杂电路布局需求,确保各功能模块间信号快速、准确传输,为用户打造舒适、便捷的驾乘体验。例如,一些高端新能源汽车的中控大屏背后,便是由多层PCB板将显示屏与多个处理芯片紧密相连,实现高清画面输出和快速的系统响应。
传感器连接:新能源汽车配备多种传感器,如毫米波雷达、激光雷达、摄像头、超声波传感器、加速度传感器等,用于感知车辆周围环境和自身状态。多层PCB板负责将这些传感器与汽车的电子控制单元连接起来,实现传感器信号的稳定传输。以77GHz毫米波雷达为例,其对PCB板的介电常数和损耗因子要求极为严苛,多层PCB板联合上游厂商开发PTFE+陶瓷填料基材,使介电常数稳定在3.0±0.05,损耗因子低至0.0015,满足高频信号传输要求,确保雷达精准探测目标物体的距离、速度和角度。对于摄像头传感器,多层PCB板通过合理布局线路,保障图像信号高速、低噪传输,为自动驾驶系统提供清晰、准确的视觉信息。
域控制器:随着自动驾驶技术向L3及以上级别发展,域控制器需集成多种传感器接口,处理海量数据,对PCB板的尺寸、布线密度和性能提出了更高挑战。多层PCB板采用HDI+Any-layer混合工艺,实现0.1mm微孔互联,在有限面积内提升布线密度30%,支撑多传感器融合的数据吞吐需求。例如,L3级以上自动驾驶域控制器的PCB尺寸普遍超过600mm×400mm,多层PCB板通过优化设计,不仅满足了大尺寸需求,还能确保各功能模块协同工作,实现对车辆行驶状态的精准判断和控制。
在新能源汽车的安全气囊系统、防抱死制动系统、电子稳定控制系统等安全关键系统中,多层PCB板承担着信号快速、准确传输的重任。以安全气囊系统为例,多层PCB板连接碰撞传感器和气囊控制器,当车辆发生碰撞时,能在极短时间内将碰撞信号传输给控制器,触发安全气囊迅速弹出,为驾乘人员提供关键保护。在ABS和ESC系统中,多层PCB板确保轮速传感器、压力传感器等信号及时传递至控制单元,控制单元据此精确调节制动压力,防止车轮抱死,保持车辆行驶稳定性,在紧急情况下保障行车安全。多层PCB板凭借良好的机械强度和电气性能,能够在车辆行驶过程中的震动、冲击等恶劣环境下,始终保持稳定工作状态,确保安全系统可靠运行。
综上所述,多层PCB板广泛且深入地应用于新能源汽车的各个关键设备,从动力系统的高效管理到智能系统的精准感知与交互,再到安全系统的可靠保障,为新能源汽车的性能提升、功能拓展和安全运行奠定了坚实基础,是推动新能源汽车技术持续进步的重要力量。
采购咨询,获取商机